- To ensure the quality, every product awaiting shipment will go through layers of strict quality inspection procedures. Only those that pass the comprehensive inspection will enter the shipping process.
After the customer receives the sample and confirms to start the mass production, we will produce a pre-production sample and communicate with the customer for confirmation again. This pre-production sample is a version that replicates and refines the details, craftsmanship, etc. based on the original sample. In the subsequent mass production process, we will strictly adhere to the standards of the pre-production sample that has been finally confirmed with the customer. From raw material procurement, manufacturing processes, to product dimensions, colors, quality control, and all other aspects, we will comprehensively ensure that the mass-produced products are highly consistent with the pre-production sample, and deliver products with stable quality and meeting the customer’s expectations.
- During the mass production process, we have set up strict quality inspection checkpoints for each process to fully ensure the product quality.
1.Strict screening of fabrics: For the fabrics used in mass production, we carefully compare them to ensure that there is no deviation from the pre-production sample. Only after confirming that the fabrics are correct will subsequent processes such as embroidery and cutting be initiated, eliminating quality differences caused by fabric problems from the source.
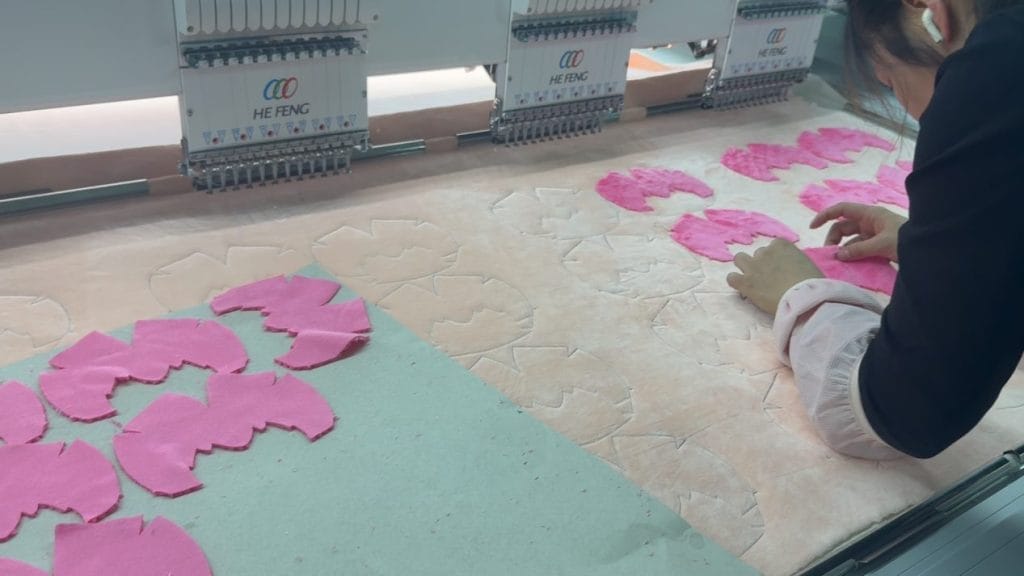
2.Thorough inspection of embroidery and cutting: We conduct a piece-by-piece check on the completed embroidery and cutting processes. We carefully examine the embroidery stitches, requiring them to be even and dense. We ensure that the pattern printing is clear and complete, and the cutting dimensions are precisely in line with the standards. We don’t overlook any minor flaws in the craftsmanship details.
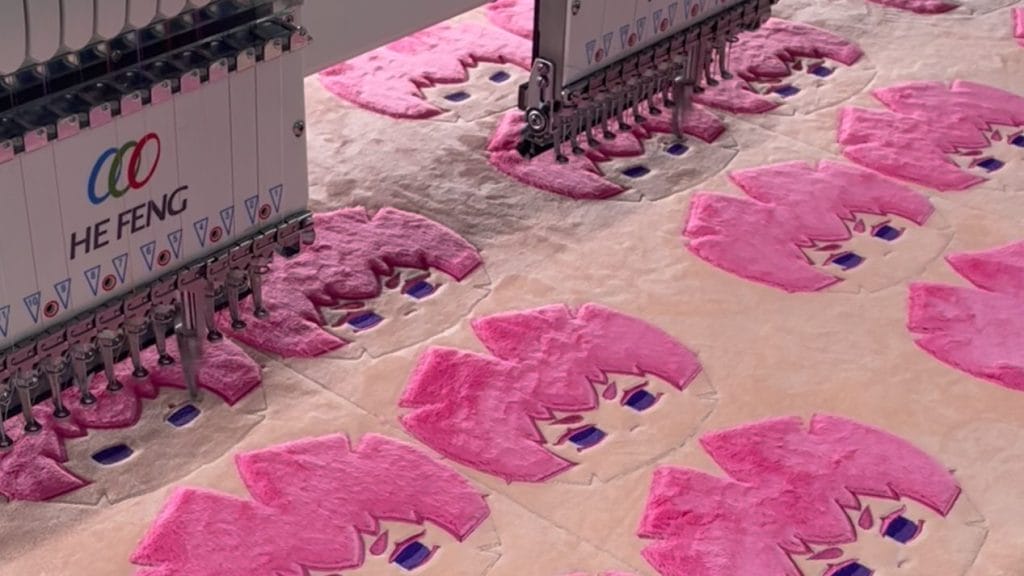
3.Control of the filling process: During the filling stage, the staff will make meticulous manual adjustments, striving to ensure that every part of the product is evenly and plumply filled. At the same time, the products will be weighed multiple times to guarantee that the weight of each finished product is consistent, presenting customers with high-quality products that feature stable quality and a uniform tactile feel.
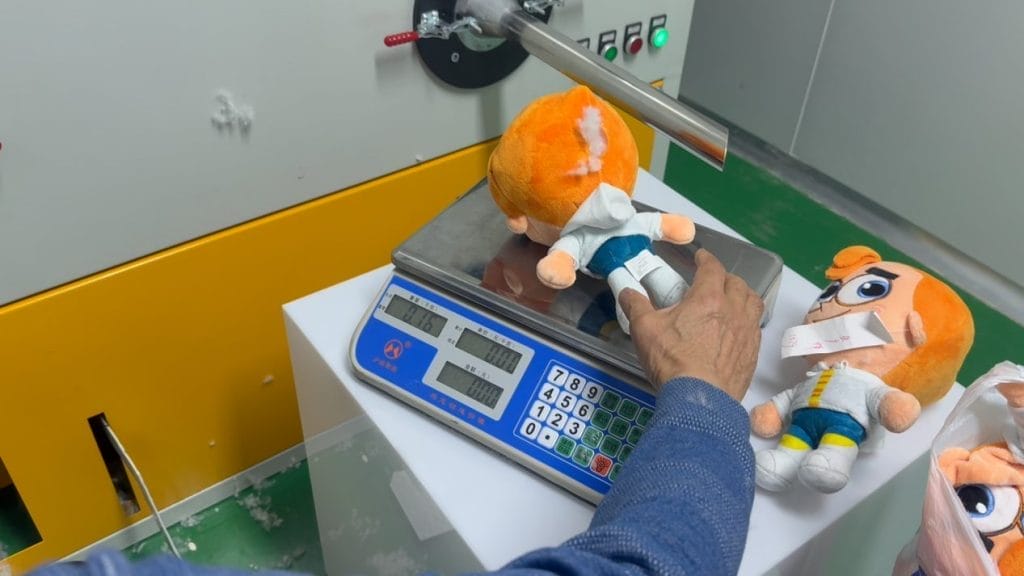
After the mass production is completed, we will conduct a final quality inspection once again:
- Dimension inspection: Measure the dimensions of the plush toy, including body length, body width, limb lengths, height, etc., to ensure that the dimensional deviation is within the range allowed by the design specifications.
- Appearance inspection: Observe whether the overall shape of the plush toy meets the design requirements. Check whether the surface of the toy is clean and free of stains and dust. If necessary, cleaning treatment should be carried out.
- Quality inspection: Check whether the embroidered part of the toy is even and dense, and whether the pattern printing is clear and complete. Ensure that the seams are firm. Examine whether the filling is plump and even.
- Safety inspection: Test the firmness of small parts. Conduct a pull test on small parts such as the eyes, nose, buttons, zippers, etc. on the toy to ensure that they are firmly attached.
- Function test: For plush toys with special functions such as sound production, light emission, electric power, or mechanical functions, conduct corresponding function tests.
- Packaging inspection: Check whether the materials used for packaging, such as cartons, plastic bags, labels, etc., meet the quality requirements. The cartons should be sturdy.
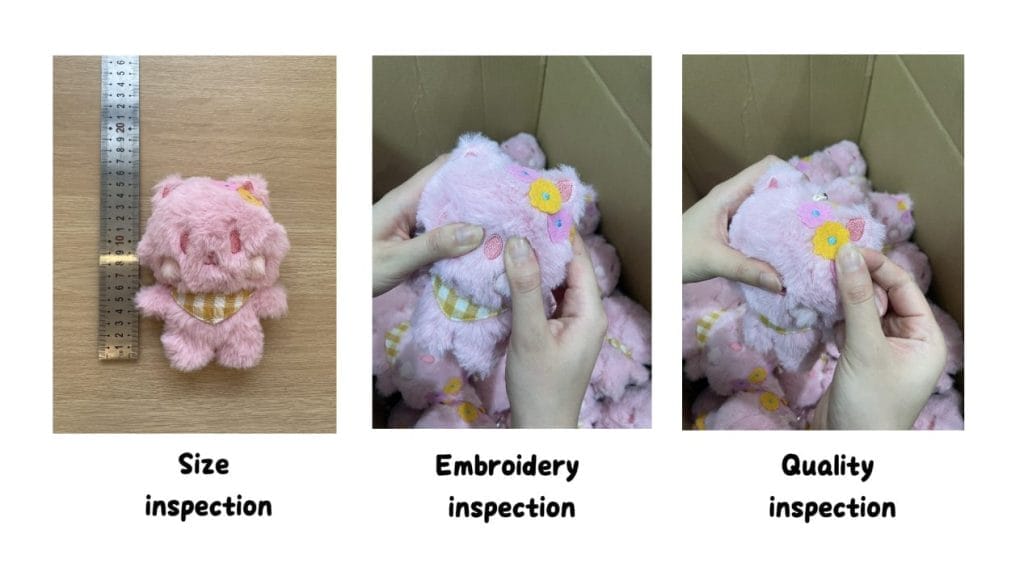
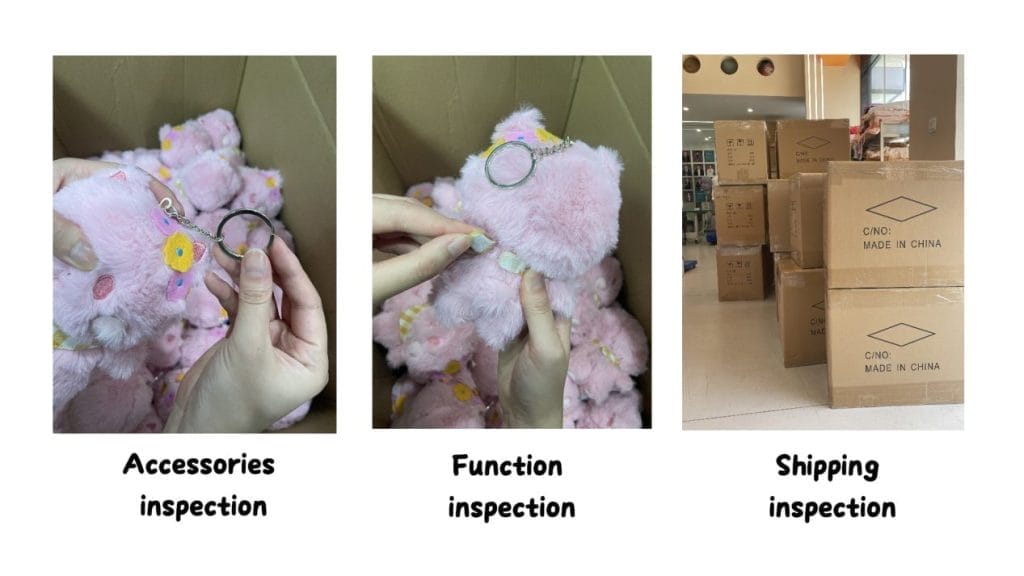
- During all the quality inspection processes, whenever defective products are found, the staff will immediately transfer them to the rework process and make adjustments and repairs in strict accordance with the standard procedures. After the repaired plush toys are completed, they will enter the quality inspection process again and undergo a comprehensive inspection. Only the products that successfully pass the quality inspection will be released, ensuring that every plush toy delivered to consumers fully meets the quality standards.
- After all the production steps have been inspected, we will take the initiative to communicate and confirm with the customer again, report the product situation in detail, patiently answer the customer’s questions, and ensure that the product status highly conforms to the customer’s expectations. Only after obtaining the customer’s explicit permission will we arrange for the shipment, and we will never act without authorization.
- After the customer receives the goods, if any problems are found, they only need to contact us immediately. Our after-sales team will respond promptly, quickly carry out problem troubleshooting, and tailor-made solutions for the customer at the fastest speed. We will follow up on the entire process until the problem is properly resolved, and we will go all out to safeguard the customer’s shopping experience.